近年來,國家對燃煤電廠產(chǎn)生的水環(huán)境影響提出了更高的要求———實現(xiàn)全廠廢水零排放,以期達到良好的環(huán)境效益和社會效益。燃煤電廠廢水回收基本上是經(jīng)過全廠水務管理及梯級利用后回用至脫硫用水,因此如何處理脫硫系統(tǒng)產(chǎn)生的高含鹽量廢水是全廠廢水零排放的關鍵。
1脫硫廢水零排放現(xiàn)狀
1.1脫硫廢水水質特點
目前燃煤電廠主要采用石灰石—石膏濕法煙氣脫硫工藝。河南發(fā)酵廢水處理,該工藝中脫硫循環(huán)漿液由于不斷吸收來自煙氣及石灰石中的氯化物,導致氯離子濃度不斷增高,其濃度的增高會帶來諸多不利影響,如:抑制石灰石的溶解,使?jié){液的pH值降低,影響二氧化硫的吸收效果,使硫酸鈣(CaSO4)易于結垢,還易導致金屬材料的腐蝕等。此外,氯離子濃度過高也會影響脫硫副產(chǎn)物石膏的品質。
為保證脫硫系統(tǒng)的正常運行,一般應控制吸收塔中氯離子含量低于20000mg/L。另外,與氯離子一樣,粉塵也會在循環(huán)漿液中不斷積累,脫硫系統(tǒng)的微細粉塵主要來自煙氣中攜帶的粉塵、石灰石中的惰性物質、停止生長的小石膏晶體及工藝水中的雜質等。為保證商用石膏的純度和系統(tǒng)漿液正常的物理化學性質,需要對系統(tǒng)內(nèi)的微細粉塵濃度進行控制。
因此,為了保證脫硫系統(tǒng)的正常運行和脫硫副產(chǎn)物石膏的品質,必須排放一定量的脫硫廢水。脫硫廢水水量、水質受煤質和脫硫系統(tǒng)工藝用水的水質影響很大,且水質和水量隨上述影響因素的變化而出現(xiàn)較大變化,基本上是一廠一水量、水質。
1.2國內(nèi)脫硫廢水零排放現(xiàn)狀
根據(jù)調研,目前國內(nèi)已實施脫硫廢水零排放的發(fā)電廠共有23家,處理水量0.5~47t/h,其中,目前已建成并且正式投運的大型燃煤電廠脫硫廢水項目情況如圖1所示。
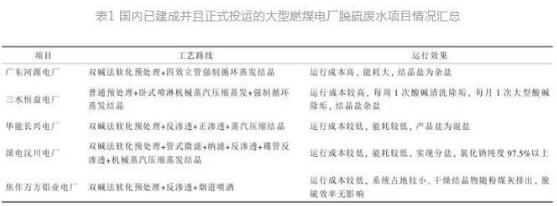
圖一
相對于傳統(tǒng)的蒸汽蒸發(fā)技術,煙氣利用技術由于利用了煙氣余熱蒸發(fā)脫硫廢水,系統(tǒng)簡單,節(jié)約占地,已越來越受到關注。
2脫硫廢水煙氣利用技術
煙氣利用技術主要有旁路煙道噴霧干燥、河南發(fā)酵廢水處理,煙道直接噴霧干燥、煙氣余熱濃縮蒸發(fā)等方法,其與機組煙氣系統(tǒng)熱平衡和各工藝段參數(shù)密切相關,以下分析這3種煙氣利用的詳細工藝特點。
2.1旁路煙道噴霧干燥工藝
該工藝原理是從脫硝系統(tǒng)出口引出熱煙氣,經(jīng)旁路煙道送至噴霧干燥塔;脫硫廢水經(jīng)管路進入干燥塔,經(jīng)過高速旋轉的霧化器霧化為細小液滴群后與煙氣進行充分的熱交換,利用煙氣余熱瞬間干燥脫硫廢水,蒸發(fā)產(chǎn)生的大部分固體物質從噴霧干燥塔底部的排放口排出;經(jīng)噴霧干燥塔干燥后的尾氣返回電除塵器進口。該工藝流程如圖1所示。
蒸發(fā)廢水需要的能量計算公式為:
式中:Mmst為需蒸發(fā)廢水的質量;T為環(huán)境溫度;T1為蒸發(fā)后蒸汽溫度;rw為水的汽化潛熱,取2262kJ/kg;cw為水的比熱容,4.187kJ/(kg˙℃)。廢水溫度T取25℃,蒸汽溫度T1取125℃,可得干化1t廢水所耗能量為3.11×106kJ。
由于脫硝出口煙氣原用于加熱進入空預器的冷風,以回收熱量,用于廢水干燥后會造成熱量損失,空預器傳熱效率按95%計,干燥1t廢水所耗熱量折合標煤100.8kg,按標煤價900元/t計,干燥1t廢水消耗的熱量折算費用約90.7元。
因此全廠脫硫廢水量較大時,可考慮先將脫硫廢水濃縮減量后再進入旁路煙道噴霧干燥,以降低整套系統(tǒng)的能耗。 河南發(fā)酵廢水處理,
脫硝出口煙氣約為350℃,干燥廢水后降至約125℃,煙氣焓降約200kJ/kg,經(jīng)計算,干燥1t廢水所需煙氣量約為15550kg,采用此工藝的各類型機組干燥脫硫廢水所需煙氣質量和占總煙氣的比值見表2(單臺機組)。
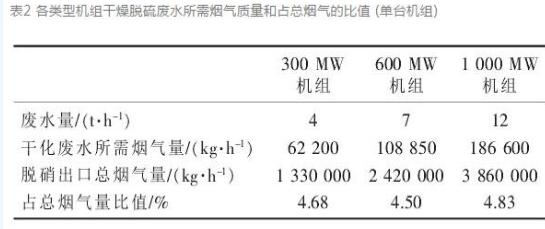
表2
從表2可以看出,理想狀態(tài)下300MW,600MW和1000MW機組單臺脫硫廢水量分別為4t/h,7t/h和12t/h。各類型機組(單臺機組)干燥脫硫廢水所需的煙氣占總煙氣量比值均接近5%。機組額定負荷時,從脫硝出口抽取約5%的煙氣會有空預器硫酸氫氨結露區(qū)跨層的風險。如采用該工藝,需要對空預器進行改造,增加鍍搪瓷段的長度。當機組處于50%THA(機組熱耗保證工況)負荷以下運行時,旁路煙氣量會相應減少,干燥塔中流場被破壞而導致廢水接觸干燥塔表面引起結垢、腐蝕,所以機組低于50%THA負荷運行時該系統(tǒng)需停運。而機組實際脫硫廢水量超過理想值,干燥脫硫廢水所需的煙氣比例超過5%,則需要經(jīng)過濃縮再進行旁路煙氣干燥。
該工藝可將廢水蒸干物混入粉煤灰中。參照典型脫硫廢水水質表,氯離子濃度按15000mg/L,飛灰含量按18g/m3計,計算結果如表3所示(單臺機組)。
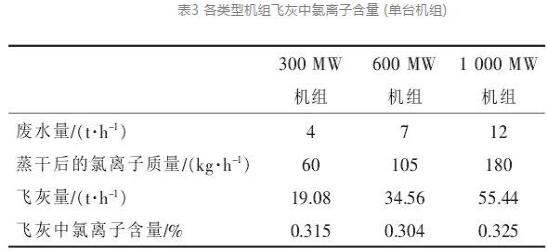
表三如圖
由表3可知,最終混入飛灰中的氯離子含量均達到0.3%以上。根據(jù)GB175-2007《通用硅酸鹽水泥》第7.1條規(guī)定,水泥中氯離子含量不大于0.06%,且水泥中粉煤灰占比約20%~40%,所以機組使用該工藝后,其粉煤灰不宜用于制作硅酸鹽水泥。但JC/T409-2001《硅酸鹽建筑制品用粉煤灰》中對用于加氣混凝土、粉煤灰磚、砌塊、粉煤灰蒸養(yǎng)陶粒及摻加粉煤灰的建筑板材等硅酸鹽建筑制品用的粉煤灰無氯離子含量要求,所以使用該工藝后,機組的粉煤灰仍可用于生產(chǎn)以上建筑制品。
該工藝的優(yōu)點是系統(tǒng)熱量利用率高,熱損失小;工藝簡單,設備少,噴霧干燥塔一般布置在靠近空預器的位置,占地比較小。
2.2煙道直接噴霧干燥工藝
煙道直噴干燥工藝是將脫硫廢水直接通過霧化噴入空預器后、電除塵器前煙道內(nèi),廢水中水分蒸發(fā)后被煙氣攜帶至脫硫塔,廢水晶體被電除塵器捕捉脫除。該工藝具有系統(tǒng)簡單、投資成本和運行費用低、對場地要求低等優(yōu)點。
根據(jù)式(1)計算可得,干化1t廢水所耗能量為3.06×106kJ。河南發(fā)酵廢水處理,各類型機組干燥脫硫廢水所需煙氣質量和占總煙氣的比值見表4(單臺機組)。
表4各類型機組干燥脫硫廢水所需煙氣質量和占總煙氣的比值(單臺機組)
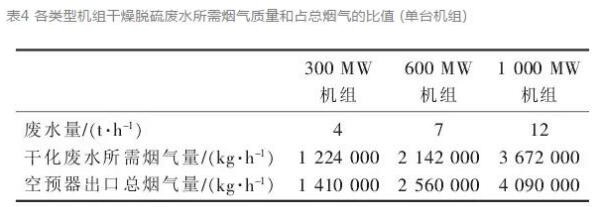
各類型機組干燥脫硫廢水所需煙氣質量和占總煙氣的比值
由表4可知,根據(jù)理想狀態(tài)下單臺機組廢水量,空預器出口的總煙氣量略大于干燥廢水所需的煙氣量,理論上如果煙氣和廢水充分接觸,可以實現(xiàn)對廢水的干燥。但由于空預器后煙氣溫度僅125℃,廢水噴入煙道后蒸發(fā)速度較慢,所以必須保證廢水與煙氣有充分的接觸時間。如果煙道距離不夠長且回轉式空預器出口煙氣流場不均勻,會出現(xiàn)局部廢水無法和煙氣充分接觸的情況,可能會有部分廢水無法在進入電除塵器前被干化。
該工藝煙氣干燥廢水后的蒸干物將混入粉煤灰中,與上節(jié)所述旁路煙氣噴霧干燥工藝的粉煤灰情況基本相同。
如機組采用低低溫電除塵器,空預器至煙氣冷卻器之間的煙道較短,可能會導致未干燥的廢水進入煙氣冷卻器,易使煙氣冷卻器發(fā)生積灰、河南發(fā)酵廢水處理,結垢造成堵塞;如果未干燥的廢水進入電除塵器,還會導致電除塵極板腐蝕。因此,設置低低溫電除塵器的機組不推薦采用煙道直接噴霧干燥技術。
2.3煙氣余熱濃縮蒸發(fā)
該工藝是利用部分電除塵器與脫硫塔之間的煙氣,將廢水在濃縮塔內(nèi)噴淋,與煙氣接觸后蒸發(fā),未蒸發(fā)的部分通過泵循環(huán)進入濃縮塔加熱,脫硫廢水在煙氣的加熱下不斷濃縮,其中的溶解物逐步達到飽和并析出,析出的物質通過板框壓濾機壓制成泥餅后外運處理。工藝流程見圖2。
根據(jù)式(1)計算可得,干燥1t廢水所耗能量為2.90×106kJ,由于所用煙氣熱量為電除塵器后的廢熱,所以該熱量不產(chǎn)生費用。電除塵器出口煙氣約為90℃,濃縮廢水后降至約55℃,煙氣焓降約35kJ/kg,經(jīng)計算,采用此工藝的各類型機組干燥脫硫廢水所需煙氣量和水份含量見表5(單臺機組)。
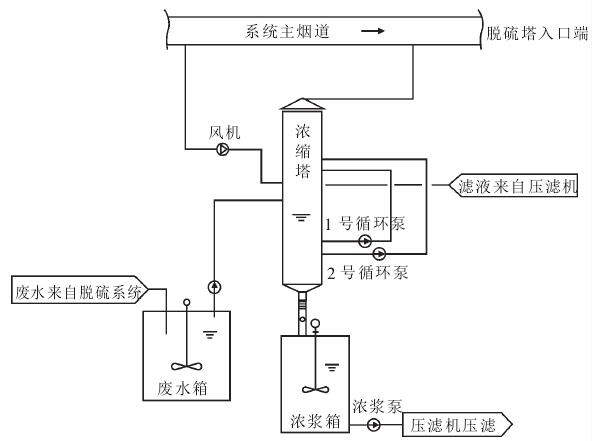
圖2煙道余熱濃縮蒸發(fā)系統(tǒng)工藝流程
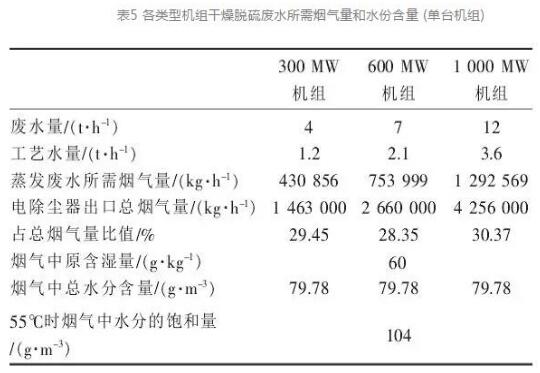
表5
由表5可知,理想狀態(tài)下抽取約30%電除塵器后的煙氣量就可以蒸發(fā)全部廢水和工藝水,并且煙氣中的水分未達到飽和,可以實現(xiàn)對全部廢水的蒸發(fā)。實際運行中廢水量超過理想值是否能夠完全蒸發(fā)還需經(jīng)過中試檢驗。
煙氣蒸發(fā)廢水后熱量減少,會減少脫硫系統(tǒng)的蒸發(fā)量,這將破壞脫硫系統(tǒng)原有的水平衡。由于不同地區(qū)的煤種和脫硫系統(tǒng)工藝用水水質不同,壓濾后的泥餅性質需要經(jīng)過鑒定。
該工藝的優(yōu)點是利用了難以利用的廢熱,直接運行費用低;工藝簡單,設備少,維護量小;廢水無需進行預處理及軟化,可直接進入該系統(tǒng)進行濃縮。
歸納總結
針對大型燃煤電廠脫硫廢水采用旁路煙道噴霧干燥、河南廢水處理,煙道直噴干燥、煙氣余熱蒸發(fā)3種技術進行研究分析,認為其共同優(yōu)點是利用煙氣熱量,熱損失小,工藝簡單設備少,運行維護量小,占地少,且3種煙氣利用技術都對處理廢水量有一定的限制。旁路煙道噴霧干燥和煙道直噴干燥方法干燥物都混入粉煤灰中綜合利用,而煙氣余熱蒸發(fā)的干燥物混入泥餅中需外運處理。
由于煙氣利用技術受機組煙氣系統(tǒng)熱量平衡及脫硫系統(tǒng)水平衡的影響,在后續(xù)具體實施過程中需結合項目煙氣系統(tǒng)和實際廢水量具體核算選擇方案。煙氣蒸發(fā)后的干燥物混入粉煤灰對粉煤灰品質造成的影響需要結合項目當?shù)鼗以C合利用情況具體分析決策。